Components
in a working
Manchette tube system:
A) The Manchette tube, B) Couplings,
C) Tips & Caps,
D) Packers, E) Packer
Rod ,
F) Connecting Valve, and G) Grout
Pump.
A
Manchette tube is a PVC or metal pipe in which rubber sleeves
cover holes that are drilled in the pipe at specific intervals.
The tubes are inserted into holes that have been bored into the
"work area" (soil, rock, concrete, etc.) known as the
"grout zone". Grout is pumped to a packer that has been
slid into the tube. Seals on the packer force the grout thru the
holes in the tube, past the flexible rubber sleeve, and into the
grout zone to help stabilize and/or seal it. Following is a more
detailed explanation of the Manchette tube system and how it works.
A)
The Manchette Tube
There are three basic categories of tubes: 1) Standard PVC Tube,
2) Recessed Rubber PVC Tube, 3) Metal Tube.
Common
among the tubes are that at every 15 inches along its length,
four holes are drilled around its circumference. The holes are
covered by a flexible rubber sleeve which allows the grout to
flow out into the surrounding environment and prevents it from
flowing back into the tube once pumping has stopped. Rubber elements
are made from a special compound which resists changes in durometer
and extensibility due to UV and temperature. All rubbers are held
in place with a light adhesive and are taped down at both ends
with electrical tape. Custom lengths of tubing can be assembled
via couplings.
Raised
Rubber Tube

This tube is constructed of schedule 40 or greater PVC pipe with
diameters of 1", 1.5" & 2" and lengths of 5
or 10 feet. The rubber sleeve is slid over, and affixed to, the
outer surface of the pipe, thus causing the outer surface of the
sleeve to be "raised" above the pipe surface. The ends
are straight cut and extended lengths are created with couplings
that slide over the outer diameter of the pipe.
Recessed
Rubber Tube
This tube is also constructed of schedule 40 or greater PVC pipe.
The rubber sleeve covering the grout exit holes sits in a recessed
groove in the PVC, made by removing a specified amount of the
pipe wall on a lathe. This causes the exterior surface of the
rubber sleeve to be flush with the exterior surface of the PVC
pipe. This is useful when sliding the Manchette tube along a horizontally
bored hole as it helps protect the rubber sleeve against damage
and prevents it from "catching" on anything as it slides
into the hole. The ends of the pipe are machined on a lathe creating
a "female" and "male" end. This allows extended
lengths to be created by simply gluing and sliding a male end
of one pipe to the female end of another. The effect of all this
is that these Manchette tubes are flush on both the inside and
outside.
Metal
Tube

This tube is similar to the other two as far as grout holes and
sleeves except, as it's name implies, it's constructed of steel.
It has a raised steel ridge on either side of the rubber sleeve.
This is used in situations similar to the Recessed Sleeve PVC
tube but is much stronger and offers more protection of the rubber
sleeve via the raised steel ridges. It comes in diameters of 1.5"
and 2", a length of 26" and a rubber spacing of 14".
Return
to Top
B)
Tube Couplings
Tube couplings, as you might guess, connect lengths of Manchette
tubes to create overall longer tubes. There are five basic types:
1) Center Stop, 2) Smoothbore, 3) Heavy Duty, 4) Extended Length,
and 5) Metal.
Center
Stop Coupling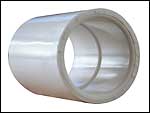
This coupling, made of PVC, connects lengths of "Recessed
Rubber" Manchette tubes. It has a small internal ridge, or
stop, midway between the ends of the coupling. This stop makes
it easier to splice two lengths of pipe in that you simply apply
glue and push the two lengths of pipe into the coupling until
they both "seat" against the stop, automatically centering
the coupling between the two pipes. Manchette tubes connected
in this manner must use an "expandable" type of packer
as the coupling leaves the two pipes with their ends slightly
separated (the width of the internal stop). Packers that have
compressed type seals will "catch" on this "space"
or "groove". These different types of packers will be
discussed later.
Smoothbore
Coupling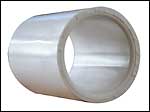
This coupling, made of PVC, connects lengths of "Raised Rubber"
Manchette tubes but has no center stop. This coupling allows the
ends of the two adjoining pipes to "butt-up" against
one another, thus creating a smooth "catch-free" bore.
This type of coupling can use either a compressed seal packer
or an expandable seal packer.
Heavy
Duty Coupling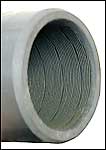
This coupling, made of heavy gauge PVC, connects lengths of
"Raised Rubber" Manchette tubes and has no center ridge,
thus creating a smooth "catch-free" bore. It also has
fine internal serrations that hold glue, thus making for a stronger
bond.
Extended
Length Coupling
These are just like the other couplings except they are
approximately 75% longer.
Steel
Coupling
Metal Manchette tubes are threaded on either end and are joined
via a threaded metal coupling. Steel couplings and tubes can only
be used with an expandable type packer.
Return
to Top
C)
Tips and Caps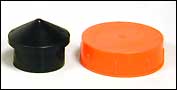
Tips are cone shaped and made of plastic. They go on the bottom
or "leading" end of the Manchette tube. The pointed
bottom tip facilitates the insertion of the tube into the bored
hole and prevents foreign matter from entering the tube. A cap
can be placed on the top or "trailing" end of the tube
to prevent foreign matter from entering the tube before grout
is pumped or between multiple applications of grout.
D)
Packers
The Packer is the device through which grout is pumped
into, and forced through, the holes in the Manchette tube. There
are two broad categories of Packers: 1. Inflatable Seal Packers,
and 2. Sliding Seal Packers.
The
two work in similar fashion; they are lowered or pushed (horizontal
tube) into the Manchette tube until the packer is halfway past
a set of the holes drilled into the tube. Grout is pumped into
the top of the packer via a connecting hose (packer rod) and grout
pump. The grout flows through the center of the top half of the
packer and exits at openings around the middle of the packer which
is approximately where the holes in the Manchette tube are. Seals
at the top and bottom of the packer prevent the grout from simply
filling the tube and pouring out the top of the tube. With no
where else to go, the grout is forced thru the holes in the Manchette
tube, past the flexible rubber sleeve into the surrounding environment
(grout zone). When the desired amount of grout has been pumped
at that particular level, the packer is slid to straddle the next
set of holes and the process continues. Following is a more detailed
look at the different packers.
Inflatable
Seal Packer

As the name implies, this type of packer has expanding rubber
seals at either end. Besides the grout hose, a second, smaller
hose is connected to the top of the packer via which air or a
liquid is pumped into the seals (with
most people preferring hydraulic inflation for speed and control),
thus expanding the seal tight against the walls of the Manchette
tube. After the grout is pumped at that level, they are deflated
in order to slide the packer to the next set of holes. There are
two types of inflatable seals:1. single chamber, and 2. multiple
chamber, both of which are capable of 1,500 psi working inflation
pressures. The multi-chamber type is modular, with exchangeable
rubber elements to change pipe sizes. The modular rubber elements
have steel rings imbedded inside the rubber which create a multiple
hourglass shape when inflated. Both types can be either single
element or two element (straddle) devices and can have varied
straddle distances (by changing out the center section) for simultaneous
multi-port injection. The single chamber type has a greater expansion
range and thus, the advantage of being able to seal a greater
range of tube diameters with just one size seal.
Sliding
Seal Packer

The seals on this type packer are slightly larger than the Manchette
tube itself and thus fit tightly against the tube walls when the
packer is inserted into the tube. There are three types of sliding
seals: 1. o-ring, 2. leather cup, and 3. poly-cup.
Mechanical
Packers
A mechanical packer is constructed of a short length of pipe with
one rubber seal around it. It normally does not use a Manchette
tube but one can be connected if necessary. Instead, a hole, slightly
larger than the packer, is bored into the grout zone (such as
a concrete wall), and the packer is inserted directly into this
hole. A threaded screw, on top of the seal, is then turned against
the rubber seal, compressing it and causing it to expand tightly
against the walls of the bored hole. Grout is then pumped thru
the packer and out the far end into the grout zone to be stabilized/sealed.
Return
to Top
E)
Packer Rod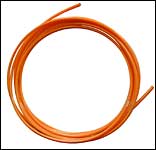
The packer rod is a tough but flexible plastic hose through which
grout is pumped to the packer. Packer Rod comes in bulk rolls
which are cut to the desired length. A threading kit allows the
user to put threads on each end of the cut hose to which couplings
are then affixed. These couplings allow the hose to be attached
to the connecting valve on one end and the packer on the other
end.
Return
to Top
F)
Connecting Valve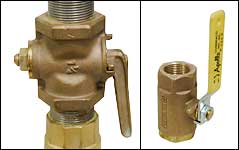
The connecting valve controls the flow of grout into and out of
the mechanical packer. There are two types: 1. Cone Valve, and
2. Ball Valve. The Cone Valve (left photo) can be quickly disassembled
and cleaned should grout set up in it. Please see our separate
section on grout pumps for more detailed
information on pumps and connecting valves.
Return
to Top
G)
Grout Pump
The grout pump does just that, pumps grout through the connecting
hose to the packer inserted in the Manchette tube. Please see
our separate section on grout pumps
for more detailed information on pumps and connecting valves.
Return
to Top